In this series, we follow a Christchurch couple in their bid to turn their 1960’s fixer-upper, from a retro rental to a modern home.
If you’ve ever considered buying an older home but have lacked the confidence to tackle something totally outdated, this guide is for you. It’s a whole lot of fun, and not as hard (or anywhere near as risky) as you might imagine.
In the previous chapter, Jason, owner-operator of Jason Ward Painter Decorator, gave the whole house several coats of fresh paint, and attended to additional details like the garage doors and spouting.
With the painting done, and the house looking ultra-fresh, it was ready for an equally fresh new kitchen and laundry. Kitchen concepts had measured and designed Jeremy and Alana’s kitchen and laundry several weeks ago – and with the manufacture now complete, it was time to install!
Before we get into the install, can you talk a little about the manufacturing process?

How did the kitchen and laundry arrive, and what challenges were there?
With their kitchen and laundry spaces freshly painted and ready for the install, we talk through the initial delivery and challenges faced.

How are imperfect walls and floors handled to achieve a perfect finish?
Before beginning the installation, it is clear that there will be fine tuning required to have the cabinets and benchtops sitting level, as well as everything sitting flush against the floor, ceiling and walls.




What other trades were needed to complete the install?
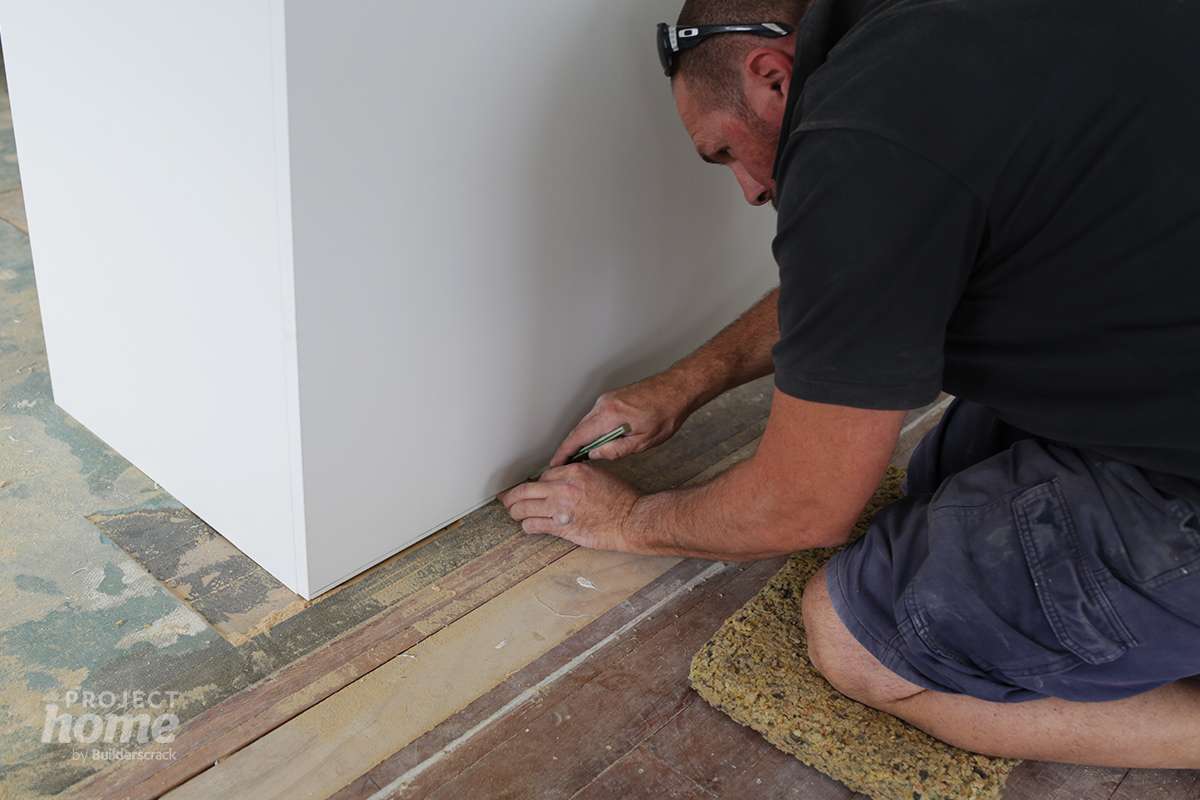