In this series, we follow a Christchurch couple in their bid to turn their 1960’s fixer-upper, from a retro rental to a modern home.
If you’ve ever considered buying an older home but have lacked the confidence to tackle something totally outdated, this guide is for you. It’s a whole lot of fun, and not as hard (or anywhere near as risky) as you might imagine.
In the previous chapter, we looked at the various window joinery and glazing options Jeremy and Alana considered, what they settled on – and how they approached the task of measuring them up.
With the window manufacture underway, it was time to bring the plumbing up to a modern standard.
Their house had a low-pressure system with header tank and galvanised plumbing, typical of a house built in the 60’s. But it’s 2019 – so time to upgrade!
Why did you touch the plumbing? Why not just leave it as is?
“Out of sight, out of mind” is how a lot of people think of their home’s plumbing. Not so with this project. Jeremy and Alana take us through why they replumbed their home as part of this renovation.

How did you decide what to do?
With their basic objectives in mind, Jeremy and Alana set out to find a plumber that understood what they wanted to achieve, could consult with them to make a detailed plumbing plan, and then make it happen quickly with proven products.
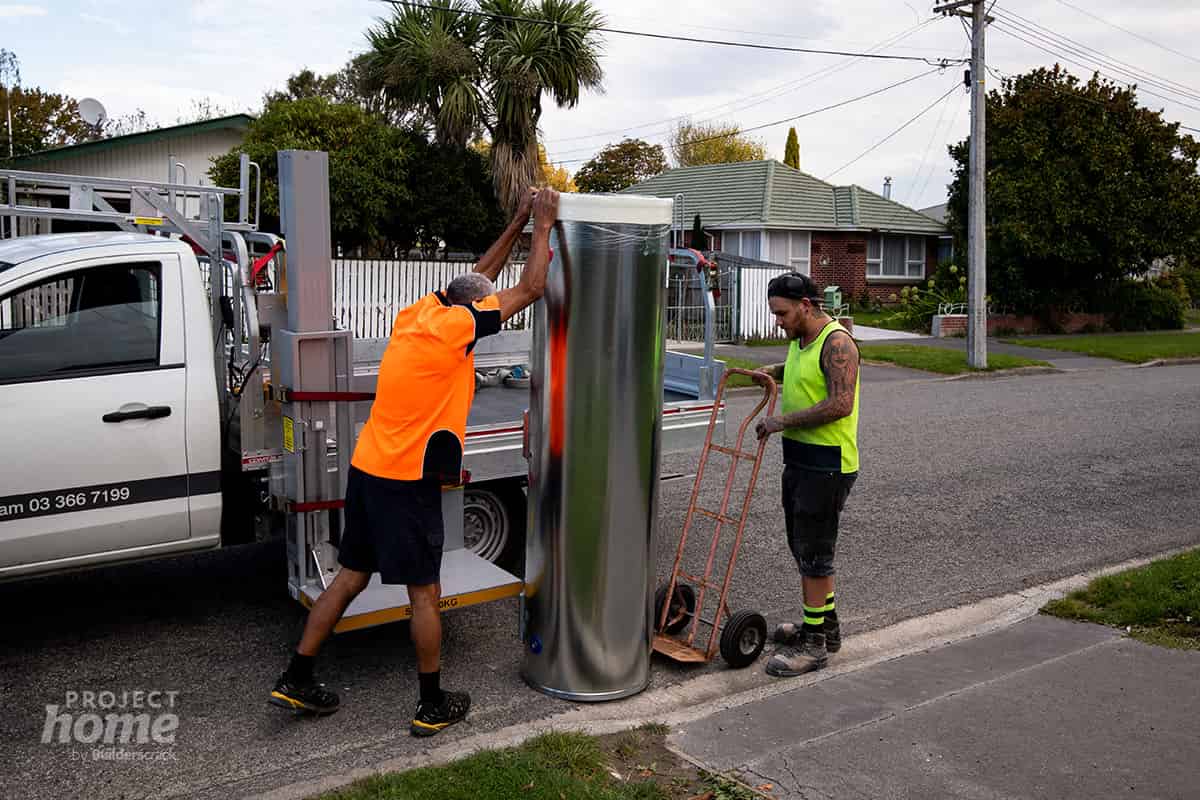
How did the plumber approach the project?
With the fine details worked through, it was time for the plumbers to get to work.

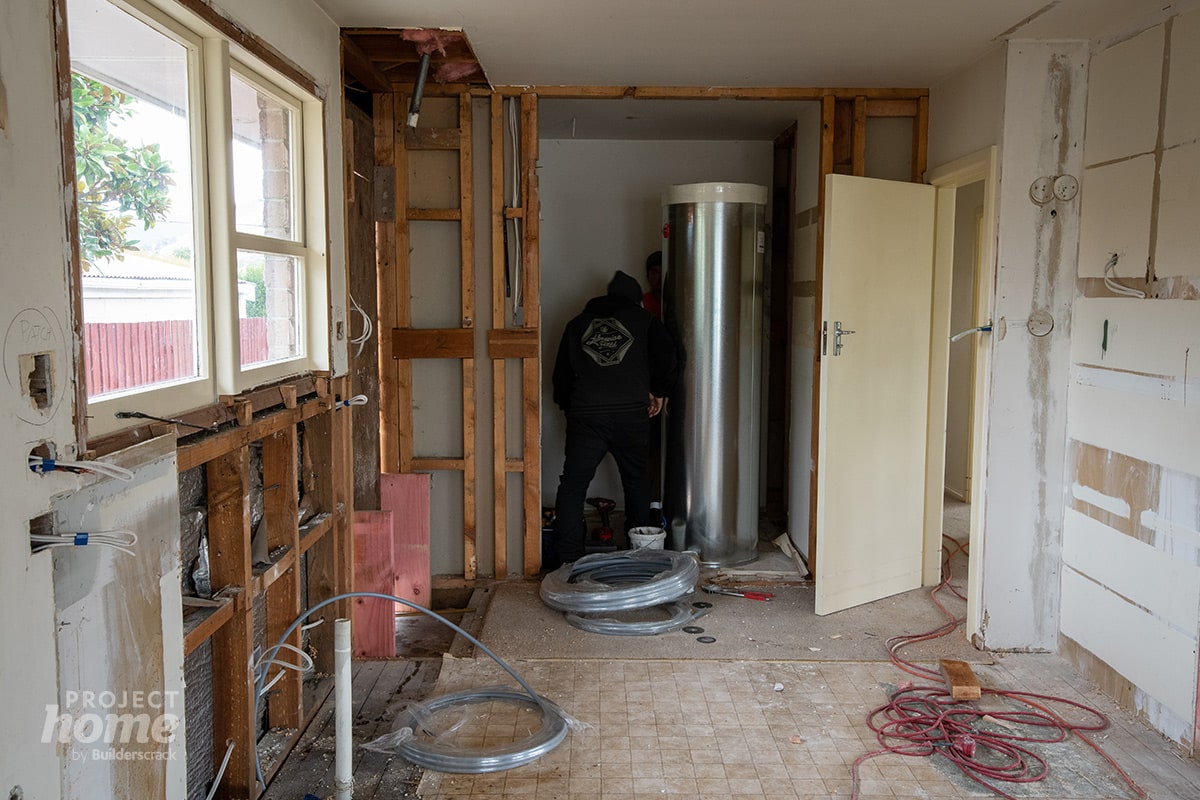

Were there any unforeseen issues?
With the plan made and the building aspects of the plumbing completed, the plumber could now get in and do the work.



