In this series, we follow a Christchurch couple in their bid to turn their 1960’s fixer-upper, from a retro rental to a modern home.
If you’ve ever considered buying an older home but have lacked the confidence to tackle something totally outdated, this guide is for you. It’s a whole lot of fun, and not as hard (or anywhere near as risky) as you might imagine.
In the previous chapter, we explored the detailed plan and looked at a typical first day of a renovation.
Now the the job-by-job plan was fleshed out, the house was electrically safe, and the demo was underway – it was time for the milimeter accurate glazing measure up.
There are a few ways to approach measuring up for double glazing. Jeremy and Alana with their builder, Mark, opted for a conservative approach. Removing all architraves (or mouldings) around the windows, and in some cases removing the windows themselves would ensure a perfect fit of the new units.
Let’s start at the beginning. What were you looking to achieve with your glazing upgrade?
As part of their renovation, Jeremy and Alana will be completely replacing all of the original single glazed timber joinery with aluminium double glazing.
Window frame material | Single glazing | IGU with 4 mm glass and 8 mm air space | IGU with 4 mm glass and 12 mm air space | IGU with 4 mm glass, 12 mm air space and low-e pane | IGU with 4 mm glass, 12 mm air space, low-e pane and argon gas fill |
---|---|---|---|---|---|
Aluminium | R0.15 | R0.25 | R0.26 | R0.31 | R0.32 |
Thermally broken aluminium | R0.17 | R0.30 | R0.31 | R0.39 | R0.41 |
Timber | R0.19 | R0.34 | R0.36 | R0.47 | R0.51 |
uPVC | R0.19 | R0.34 | R0.36 | R0.47 | R0.51 |
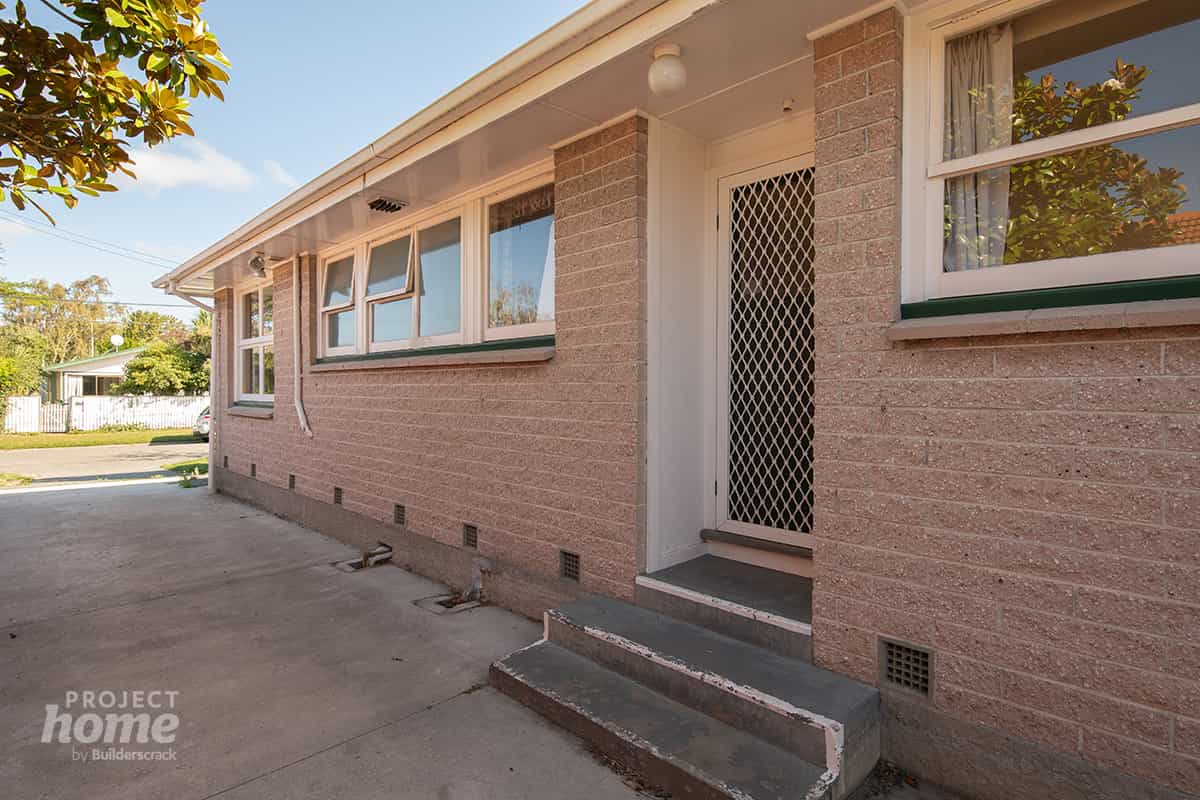
What joinery and glazing did you opt for and why?
After a process of researching different glazing and joinery options, Jeremy and Alana measured up their windows and sent off their measurements to various manufacturers. They received quotes back, and were ready to decide on a solution.

How did the window maker work with the builder to get the right fit?
Now that Jeremy and Alana had settled on a glazing and joinery solution, and found a manufacturer – they needed the window maker and the builder to work together to ensure everything was a perfect fit.
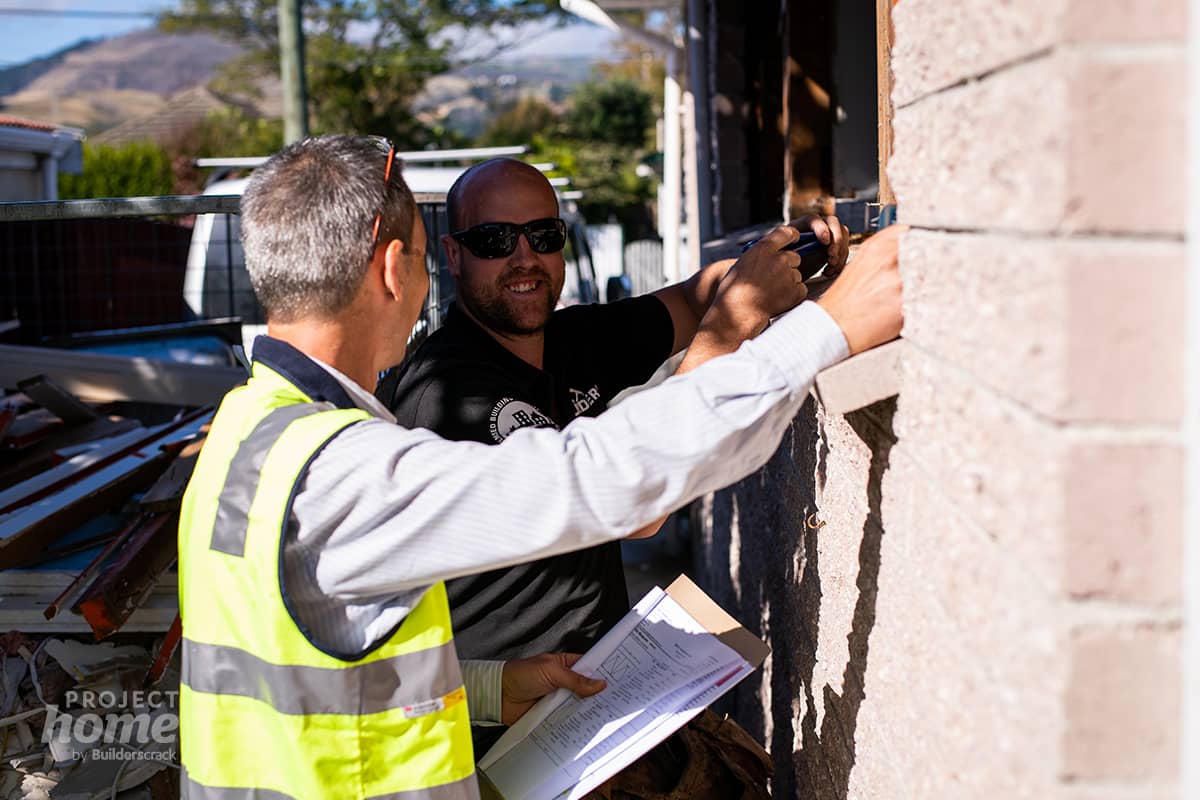


What was the process from there?
All window and door openings had been measured, and the manufacture was now underway, with a two week turnaround.



