In this series, we follow a Christchurch couple in their bid to turn their 1960’s fixer-upper, from a retro rental to a modern home.
If you’ve ever considered buying an older home but have lacked the confidence to tackle something totally outdated, this guide is for you. It’s a whole lot of fun, and not as hard (or anywhere near as risky) as you might imagine.
In the previous chapter, we met with Glen from Kitchen Concepts, who worked with Jeremy and Alana to design and make the kitchen of their dreams.
With the kitchen design settled and the manufacture underway, it was time to focus back on the house. Mark (the builder) and his guys had made great progress and it was now time to take delivery of the new double glazed windows.
Installation would take 4-5 days. Mark and his team would work window-by-window, door-by-door, removing and replacing each with the new units.
What work was involved with the window/door replacements?
In Chapter 5, we looked at the glazing measure and choices. Jeremy and Alana had chosen aluminium double glazing to replace their timber single glazing. The new units were ready and it was time to get stuck in.


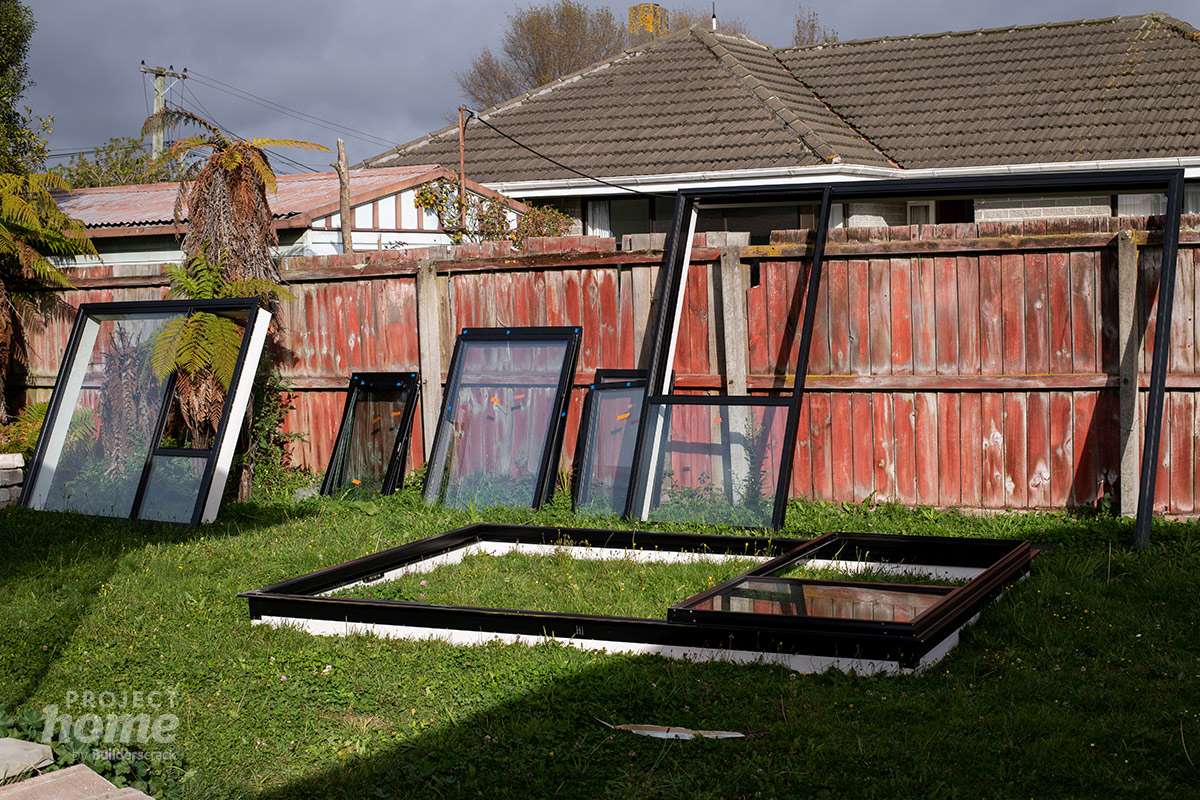
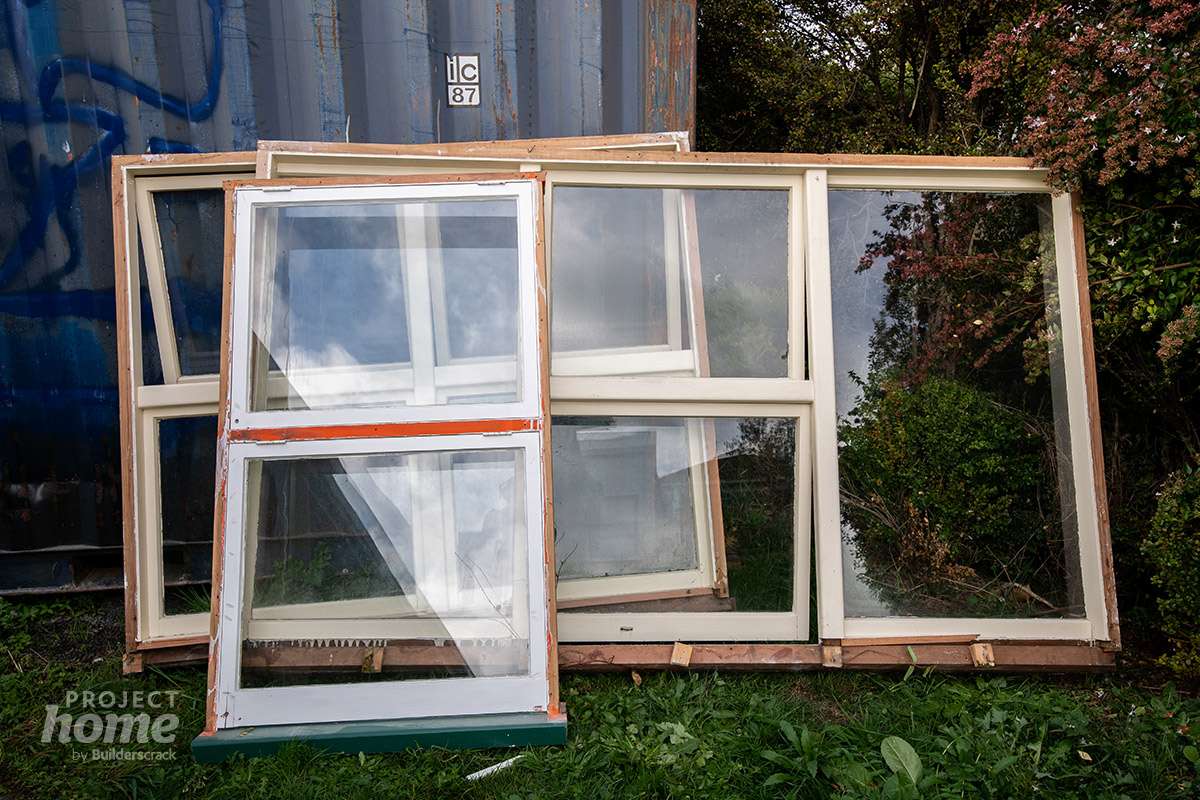
Were there any tricky bits?
While most of the window replacements were fairly straightforward like-for-like, the sliding doors were taller than the original window openings and would require some additional work.
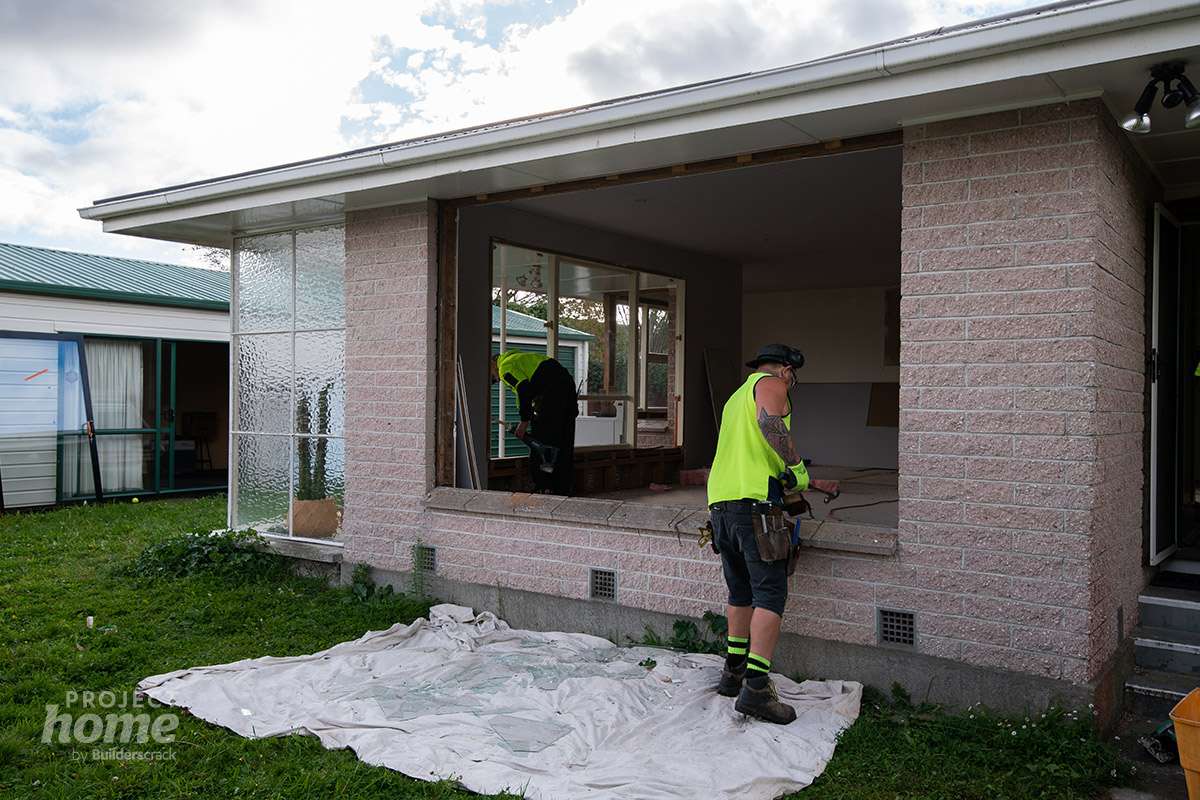
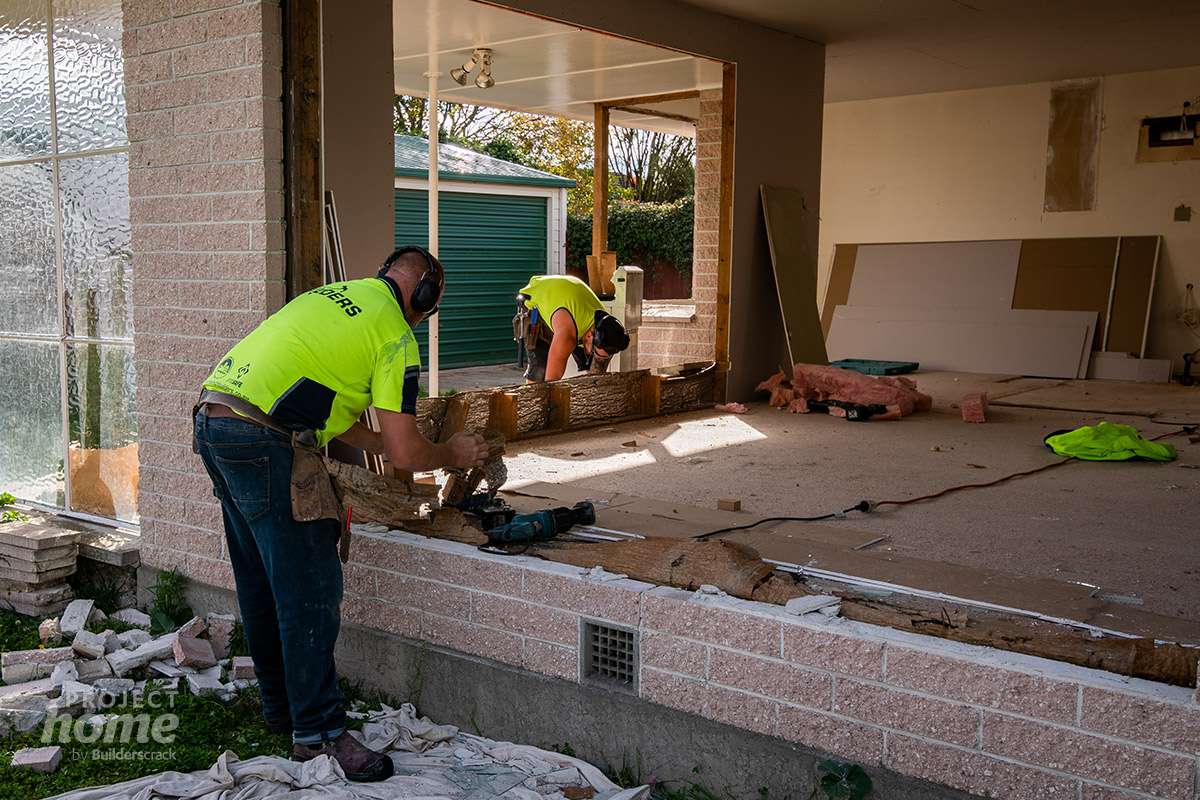



What was the process for removing the windows?




Did the result meet your expectations?
With the windows and doors now replaced, the majority of the building work was now completed. We discuss where the reno is at, and how Jeremy and Alana were feeling now that this milestone had been achieved.


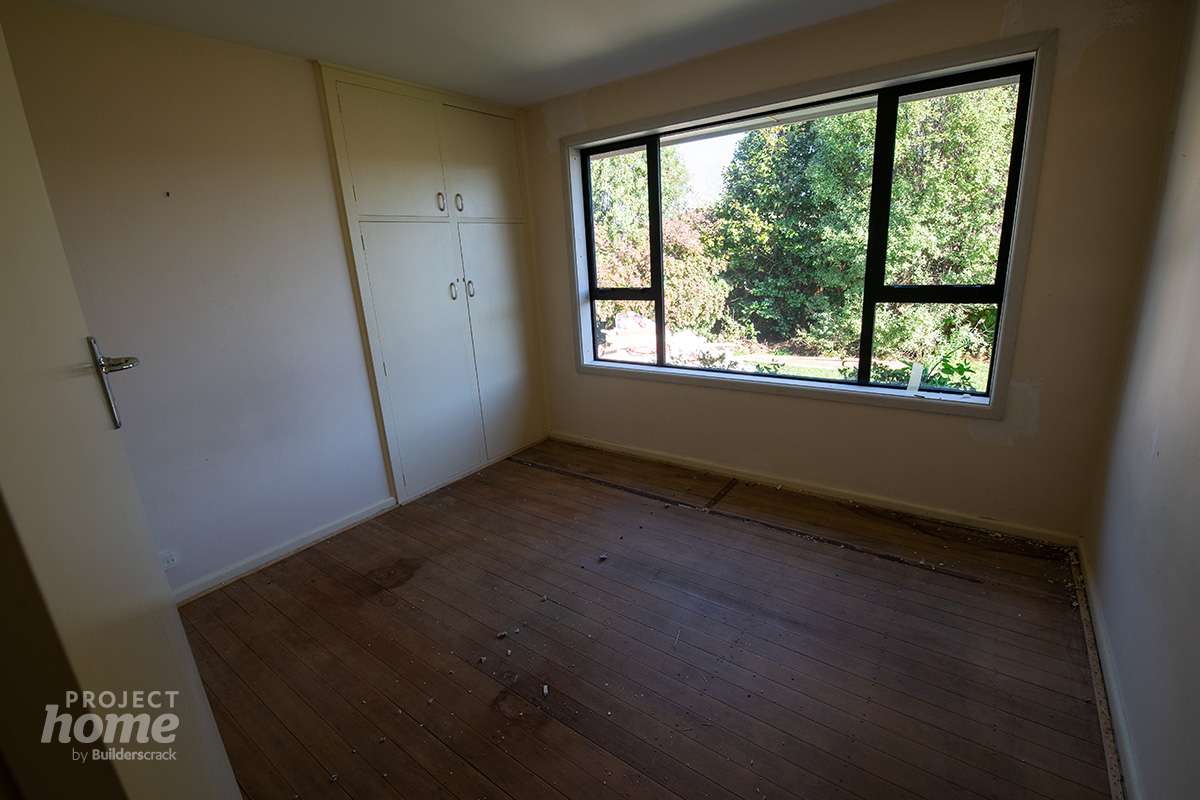
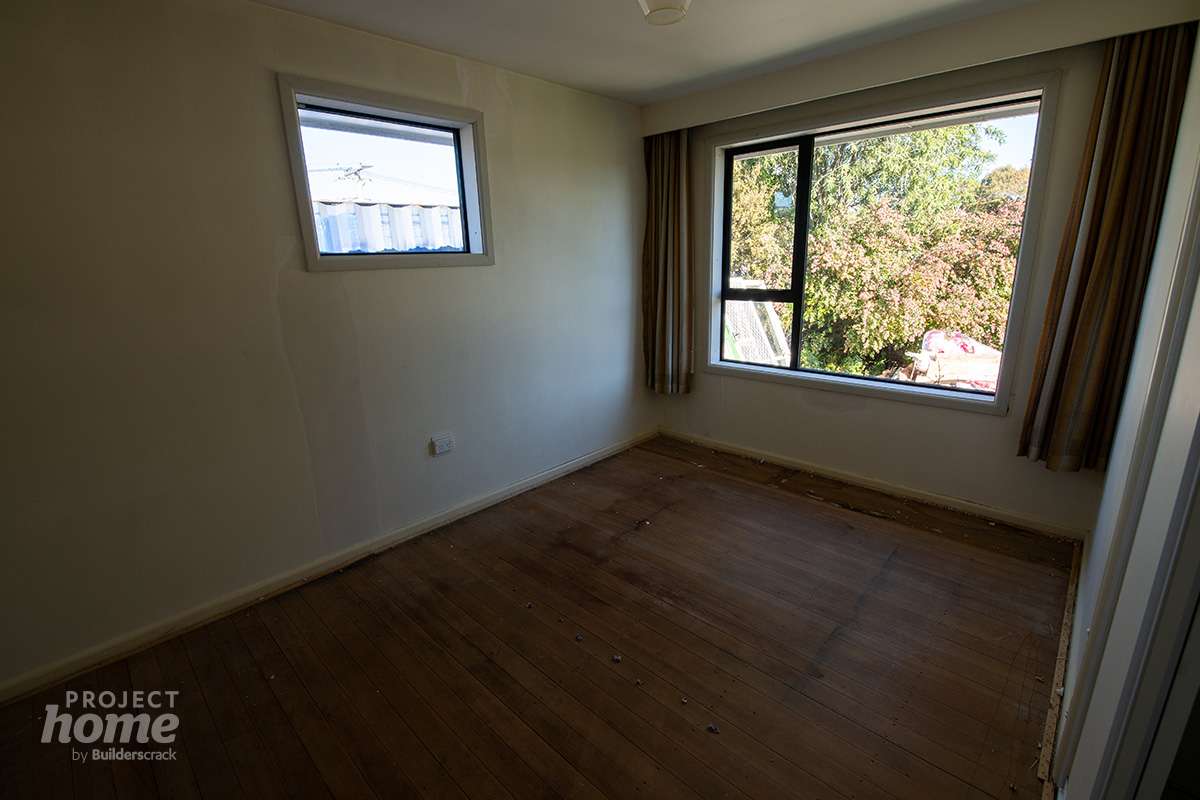